Projekt MADE4LO to drukowanie 3D z metalu made in Lombardy
MADE4LO (Metal ADditivE for Lombardy) to projekt powołany do życia przez przedsiębiorców z Włoch ze względu na wymogi stawiane przez Przemysł 4.0. Powstał dzięki grupie największych lombardzkich zakładów produkcyjnych, uczelni i włoskich organizacji technicznych. W czasie trwania projektu, sfinansowanego częściowo przez region Lombardia, opracowano nowe rozwiązania wykorzystujące procesy druku 3D z metalu.
Cechą wyróżniającą tę inicjatywę jest fakt, że wszystkie procesy i maszyny wykorzystane do produkcji 3D w ramach MADE4LO są w całości dostarczane przez lombardzkie firmy. Podzieliły się one swoim know how oraz zasobami w celu wypracowania całego cyklu produkcyjnego elementów metalowych metodą przyrostową.
PRZECZYTAJ RÓWNIEŻ: Adoptuj bezdomną czaszkę z Neapolu
Jako technologia wspomagająca, wytwarzanie przyrostowe (Additive Manufacturing, nazywane także drukiem 3D) jest jedną z technologii charakteryzujących Przemysł 4.0. Można w ten sposób produkować obiekty o skomplikowanej budowie, które powstają poprzez nakładanie (drukowanie) kolejnych warstw materiału. Jest więc przeciwieństwem metody ubytkowej (np. frezowanie czy wiercenie). Druk 3D zapewnia większą elastyczność produkcji i pozwala wytwarzać złożone elementy w krótszym czasie. Ponadto, umożliwia wyprodukowanie tylko jednego elementu w sytuacji, gdy jest on akurat potrzebny.
Druk 3D i fabryka rozproszona made in Lombardy
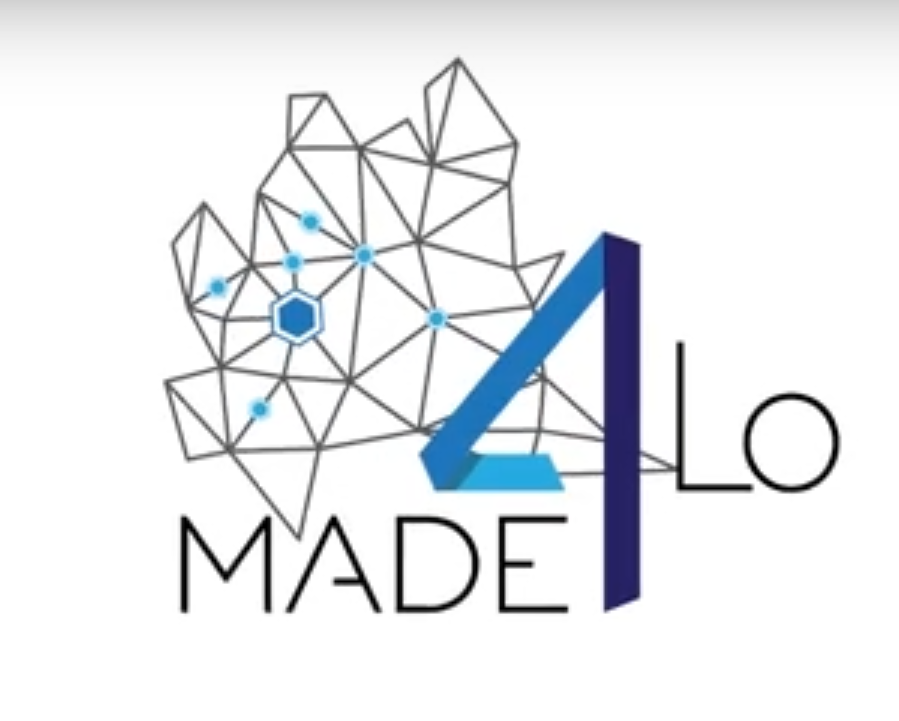
MADE4LO to inicjatywa grupy włoskich przedsiębiorstw przemysłowych, uczelni i organizacji technicznych z Włoch, działających wspólnie w ramach lombardzkiego stowarzyszenia AFIL (Associazione Fabbrica Intelligente Lombardia). Celem stowarzyszenia są działania na rzecz badań, rozwoju i innowacji w sektorze nowoczesnej produkcji. W strukturach stowarzyszenia wyodrębniła się grupa robocza złożona z kilkunastu firm oraz dwóch włoskich uczelni wyższych. W ramach tej właśnie grupy, w roku 2017, uruchomiono innowacyjny projekt MADE4LO.
Celem całego przedsięwzięcia było utworzenie pełnego łańcucha produkcyjnego dla procesu drukowania 3D z metalu: od wyprodukowania metalowego proszku do drukowania komponentów, poprzez produkcję właściwą, czyli wytworzenie części metodą addytywną (również z kilku materiałów), następnie obróbkę cieplną i hybrydową obróbkę wykończeniową (przyrostową i ubytkową), aż po próby funkcjonalne.
Założeniem projektu MADE4LO było więc utworzenie we Włoszech tzw. fabryki rozproszonej (po włosku fabbrica diffusa) i opracowanie technologii oraz procesów druku 3D z metali całkowicie made in Lombardy. Niemałe znaczenie ma również fakt, że inicjatywa uwzględniała wymogi stawiane produkcji zrównoważonej, przyjaznej środowisku.
MADE4LO: nowe wyzwania Przemysłu 4.0, nowe patenty, nowy design komponentów
Projekt o wartości 6,6 miliona euro (z czego region Lombardia wyłożył 3,5 miliona) koordynowała Tenova. Spółka z Grupy Techint specjalizuje się w rozwiązaniach inżynieryjnych dla przemysłu metalurgicznego i wydobywczego. Trwający dwa i pół roku projekt zaowocował uzyskaniem dwóch patentów. Przeprojektowano również dwa komponenty i zoptymalizowano je w taki sposób, aby można je było drukować.
Jednym z tych elementów był wtryskiwacz tlenu do pieców łukowych, wykonany z czystej miedzi w technice selektywnego topienia laserem (SLM).
Drugim była rura układu wydechowego włoskiego motocykla, wydrukowana w procesie napawania laserowego (LMD). W przypadku rury, o trudności przedsięwzięcia stanowiły jej gabaryty. Gotowa część ma długość 450 mm, a jej drukowanie trwało 12 godzin.
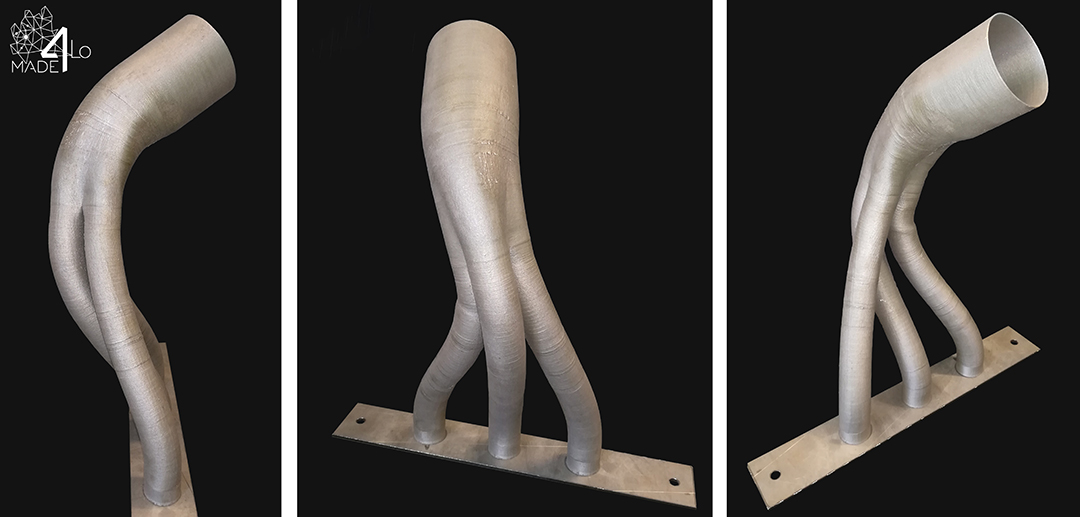
Osiągnięcie sukcesu było możliwe dzięki współpracy z Uniwersytetem w Pawii oraz z Politechniką w Mediolanie. Uczelnie udostępniły swoje przestrzenie laboratoryjne wyposażone w najnowocześniejszy sprzęt do badań i rozwoju druku 3D.
MADE4LO konkretnie: historie innowacyjnych komponentów drukowanych z metalu
Abb: metalowy rozpraszacz ciepła z drukarki 3D Streparava: korbowody i wałki rozrządu spersonalizowane dzięki wytwarzaniu przyrostowemu GFM srl: komponenty naprawiane metodą przyrostową Camozzi: fokus na czujniki Tenova: recykling proszku z części brakowych
ABB Italia: rozpraszacz ciepła produkowany w technologii druku 3D z metalu
Włoski oddział koncernu działającego w branży robotyki, automatyki i energii ma w Lombardii duży zakład produkcyjny w miejscowości Dalmine (Bergamo). Dzięki udziałowi w projekcie MADE4LO, ABB Włochy zmierzyła się z wyzwaniem wyprodukowania rozpraszacza ciepła (radiatora) metodą wytwarzania przyrostowego. Urządzenia tego rodzaju są zazwyczaj zbudowane z kilku części. ABB natomiast chciała uzyskać jeden korpus. Plan działania celował w zredukowanie wagi oraz zwiększenie powierzchni w celu poprawienia wydajności.
Ambitny plan ABB obejmuje digitalizację, automatyzację i wdrożenie nowych technologii, czego kulminacją ma być całkowita integracja łańcucha dostaw. Z tej perspektywy, wdrożenie technik produkcji przyrostowej, umożliwiającej drukowanie zaawansowanych produktów we własnym zakresie oraz w chwili, gdy są potrzebne, bez konieczności utrzymywania zapasów magazynowych, to krok o ogromnym znaczeniu. Problem leży w tym, że ta metoda nie nadaje się jeszcze do produkcji seryjnej. Jednak celem fabryki ABB, która zyskała we Włoszech prestiżowe miano Impianto Faro (tzw. Lighthouse Plant, czyli fabryki pełniącej rolę innowatora przynoszącego korzyści całej wspólnocie produkcyjnej oraz będącej technologicznym punktem odniesienia) jest właśnie przekroczenie progu niewielkich partii produkcyjnych.
Streparava: wytwarzanie przyrostowe pozwala spersonalizować korbowody i wałki rozrządu
Streparava SpA to spółka z Brescii produkująca części mechaniczne do silników i podwozi. Jest również znana na arenie międzynarodowej ze swoich zawieszeń, które sprzedaje do 30 krajów. W ramach MADE4LO firma przetestowała dwa rozwiązania wykorzystujące do produkcji komponentów automotive druk 3D z metalu: selektywne topienie laserowe (SLM selective laser melting) oraz napawanie laserowe (LMD laser metal deposition, znane również pod nazwą laserowe osadzanie metalu).
Pierwszą metodę wykorzystuje się do produkcji części poprzez wypalanie warstw proszku metalu laserem o wysokiej mocy i skupionej wiązce. W wyniku zastosowania tej techniki, Streparava przeprojektowała korbowód z tytanu: teraz jest lżejszy o 15% od oryginalnego, przy zachowaniu doskonałych parametrów mechanicznych. Natomiast drugą technikę druku 3D z metalu (LMD, gdzie nie ma warstw, lecz energia cieplna lasera topi obrabiany element, do którego jest jednocześnie doprowadzany metalowy proszek, który również się topi i łączy z drukowaną częścią) wykorzystano do produkcji nowego wałka rozrządu o spersonalizowanych parametrach.
Spółka chce nadal podążać w tym kierunku, aby zyskać elastyczność w dostawach produktów i usług o wysokiej wartości dodanej. Wszystko oczywiście zgodnie ze specjalizacją i wyjątkowym charakterem sektora przemysłowego Lombardii.
GFM srl: naprawy techniką przyrostową pomogą uratować uszkodzone komponenty
Lombardzka spółka GFM srl postawiła na udoskonalenie procesów naprawy części. Za cel obrała odzyskanie za pomocą techniki przyrostowej kosztownych, uszkodzonych komponentów, takich jak np. łopatki turbin. Możliwość wykorzystania cyfrowego bliźniaka uszkodzonej łopatki jest kusząca. Wydrukowana w 3D część może się bez problemu wpasować funkcjonalnie po ponownym montażu. Taki proces jest złożony i zdecydowanie warto go wdrożyć.
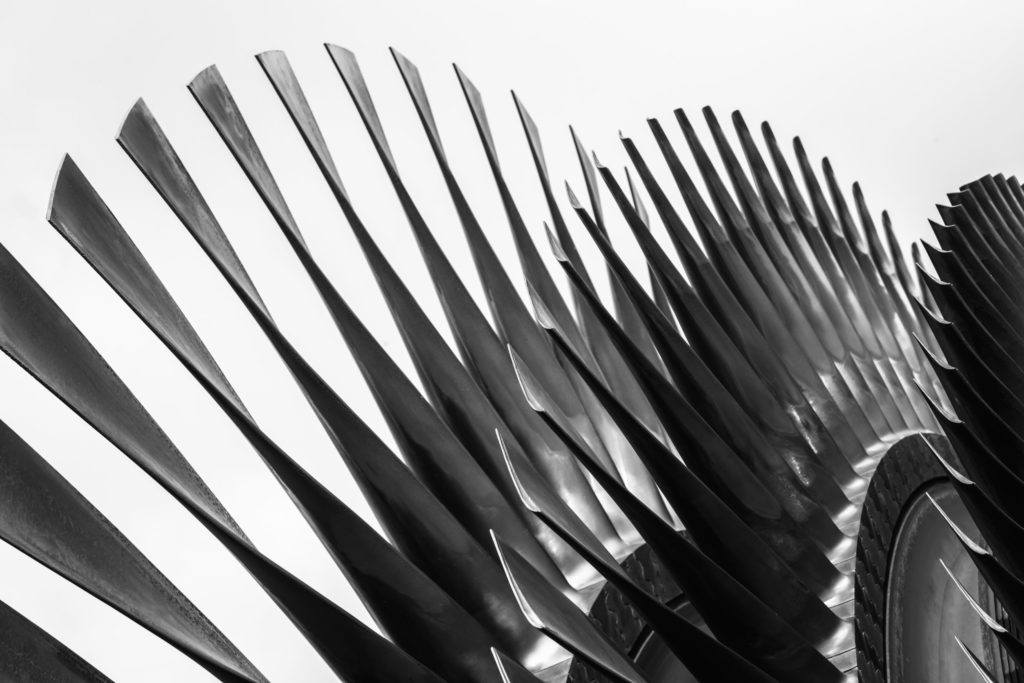
Produkcja addytywna to pole, na którym GFM srl działa już od jakiegoś czasu. Zaangażowanie firmy w tym obszarze dało konkretne rezultaty. W ramach MADE4LO otworzono we Włoszech ATC, Attitive Technology Center, w miejscowości Nembro, w prowincji Bergamo. Ten włoski hub technologiczny dysponuje najnowszymi maszynami DMG Mori, wśród których perełką jest Lasertec 65 3D Hybrid, łącząca wytwarzanie przyrostowe w technice SLM oraz frezowanie wykańczające części.
GFM srl to firma z siedzibą w Mapello (Bergamo). Specjalizuje się w projektowaniu, prototypowaniu, produkcji, obróbce i montażu precyzyjnych elementów mechanicznych ze wszystkich rodzajów stali oraz stopów zwykłych i specjalnych. Produkuje przede wszystkim części do turbin gazowych, a od niedawna rozpoczęła przygodę z aeronautyką. Często są to elementy bardzo trudne w produkcji i delikatne, takie jak uszczelki o grubości kilku dziesiątych milimetra.
Camozzi: technologie czujnikowe do zbierania danych podczas procesu wytwarzania przyrostowego komponentów o bardzo dużych gabarytach
Dla Camozzi Automation najważniejsze jest drukowanie przyrostowe części o dużych gabarytach, ponieważ w produkcji takich właśnie komponentów firma się specjalizuje. Kolejnym obszarem, na którym skupia swoją działalność są systemy czujnikowe zbierające dane w trakcie druku 3D. Te rozwiązania przydają się do zapobiegania zatrzymaniom maszyny.
Camozzi to włoskie przedsiębiorstwo z sektora produkcji komponentów i systemów do automatyki przemysłowej. Operuje również w branży obrabiarek oraz w licznych innych procesach obróbczych surowców. Mocno działa też w sektorze wytwarzania przyrostowego. Dzięki nabyciu amerykańskiej Ingersoll, światowego dostawcy maszyn do produkcji przyrostowej i ubytkowej dla branży lotniczej i kosmicznej, obronnej, energetycznej i wszystkich sektorów mechaniki ciężkiej, Camozzi zdobyła specjalistyczny know how dla maszyn dużych i bardzo dużych, drukujących z tworzyw termoplastycznych lub z kompozytów.
Największa drukarka 3D na świecie
Dziś Camozzi Automation produkuje największe drukarki 3D na świecie. Obrabiają one elementy o gabarytach 6x4x2 m. Są to przede wszystkim maszyny hybrydowe, które frezują równocześnie w pięciu osiach i są wykorzystywane zwłaszcza w przemyśle lotniczym i kosmicznym.
Tenova: produkcja proszków z metalowych braków lub z części po recyklingu
Sprawująca nadzór nad całym projektem Made4Lo Tenova SpA specjalizuje się w rozwiązaniach inżynieryjnych dla przemysłu metalurgicznego i wydobywczego. Spółka opracowała i rozwinęła technologię związaną z wytwarzaniem przyrostowym, która zapewnia dostępność niezbędnego materiału roboczego, czyli metalowego proszku. Opatentowane rozwiązanie polega na topieniu metalowych elementów (pozyskanych z braków lub z recyklingu) w piecach łukowych (EAF). Ciekły materiał przechodzi odpowiednią obróbkę w piecach próżniowych. Następnie można go rozdrobnić w celu wyprodukowania metalowego proszku przeznaczonego do produkcji metodą addytywną.
Tym sposobem, również początkowy etap łańcucha produkcyjnego pozostaje w obrębie regionu Lombardia i cały cykl produkcyjny się zamyka.
MADE4LO potwierdza wiodącą rolę Lombardii w Przemyśle 4.0 Włoch
MADE4LO to jeden z najważniejszych projektów włoskiego Przemysłu 4.0 ostatnich lat. Potwierdził również wiodącą rolę Lombardii jako filaru drugiego sektora włoskiej gospodarki. Włosi ponownie potwierdzili, że jak się postarają, to potrafią.
Utworzenie fabryki rozproszonej, czyli kompletnego łańcucha produkcyjnego dla druku 3D skupionego na jednym obszarze, było nie lada wyzwaniem. Podczas spotkań roboczych zmierzono się nie tylko z problematyką samego druku 3D z metalu. Równie mocny nacisk położono na design wytwarzanych przyrostowo elementów. Oprócz tego, opracowano i wdrożono specjalnie dedykowane oprogramowanie CAM w środowisku Siemens NX, dzięki czemu prace badawcze były w ogóle możliwe.
Projekt przebiegał wg wytycznych stawiających na gospodarkę zrównoważoną, na ochronę środowiska oraz na aspekty społeczne.